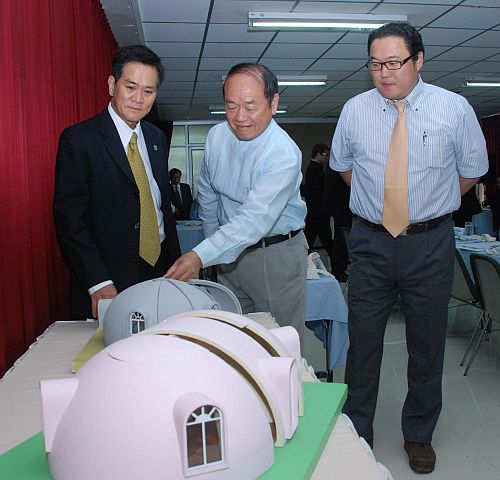
From left to right: Prof. Worsak Kanok-Nukulchai, Mr. Katsuyuku Kitagawa, and Mr. Shuji Okumoto view a miniature replica of an IDH prefabricated dome house.
housing.Asiafrica Foundation President and AIT adjunct faculty member, Dr. Roland Amoussou-Guenou, said that Thailand could very well repeat its success of exporting rice to Africa by exporting housing technology. He also suggested that AIT could take the lead for capacity building and research.
The event attracted the participation of senior executives of International Dome House (IDH), Japan, as well as representatives of Thai firms Thai Design Consortium, Thai Center of Standard Engineering, Shera, and the Habitech Center of AIT.
Africa’s housing needs are vast, seminar-goers were told. The continent is home to more than 1 billion people and in its towns and cities less than 10 per cent of people live in decent housing. UN Habitat estimates that 7000 new houses a day are needed in Africa to cope with rapid urbanization and the lack of adequate housing.
During the discussions, Prof. Worsak noted that securing workable government-to-government arrangements would be the key to mitigating export risks for Thailand’s engineering firms. Panelists representing both the private and private sector agreed.
“The only way to solve the problem is Africa is to introduce prefabrication systems,” said Mr. Vichit Chinalai, President of TDC, stressing that existing Thai technology could make a difference in Africa. He said that with the right state-backing, his affiliated consortium of firms could easily introduce 15,000 housing units into Africa each year.
“South Africa is facing a huge backlog in housing,” Mr. Velelo G. Kwepile, Political Counselor representing the Embassy of South Africa to Thailand, said as he encouraged potential partners from Africa, Thailand and Japan to emphasize the local cultural and climatic conditions when proposing housing solutions.
Mr. Geoffrey Chima, Counselor, representing the Embassy of Nigeria to Thailand emphasized that people’s access to land and financing presented big challenges. He called on the private sector to transfer its housing technology to Africa to facilitate long-term development growth.
Arriving from Japan, IDH exhibited a miniature display of its Dome House technology based on Expanded Polystyrene (EPS). Apart from possessing a number of so-called “world first” attributes, the 800-kg environmentally-friendly prefabricated homes could be assembled in 3-hours, company representatives said. “Introducing one million units per year into Africa is possible,” said Mr. Katsuyuki Kitagawa, IDH CEO and President.
Though not a prefabrication technology, the cost-effective and sustainable housing construction system developed by AIT's Habitech was presented as a suitable approach for Africa by its director Mr. Gyanendra Sthapit. He said Habitech’s interlocking bricks made from local soils have proved successful when introduced at sites in Nepal,
Bhutan, and Myanmar.
Mr. Sthapit illustrated the example of the southern Thailand village of Ban Nam Khen, which was devastated by the 2004 Indian Ocean tsunami, where numerous 74 square-meter two-storey homes were constructed for as little as US$ 7,500 each. Interlocking brick construction offers numerous advantages, he told the seminar. Homes are constructed directly on site by local people who needn't be skilled labor. The process is simple and fast, he said, and the technology is completely environmentally-friendly. He added that it requires no use of energy, apart from human labor.
“Unless there is real grassroots participation, the housing problem cannot be solved,” Mr. Sthapit explained, pointing out that Habitech’s sustainable construction system benefits communities through a fully bottom-up, participatory process.
Earlier Dr. Faiz H Shah, Head, Development Management, AIT Extension, welcomed the participants.
Dr. Roland Amoussou-Guenou (right)
addressing delegates at the seminar on “Asian Prefab Technology for
Budget Housing.”